Establishing a zero defect control loop in manufacturing as part of the Qu4lity project
18. 10. 2021
As part of the European Qu4lity project for Zero Defect Manufacturing (ZDM) in Industry 4.0, Kolektor's KiS 4.0 machine vision platform provides advanced features for state-of-the-art quality control based on visual information and artificial intelligence. The final goal of Kolektor's project team is to develop intelligent quality control agents and build a ZDM control loop.
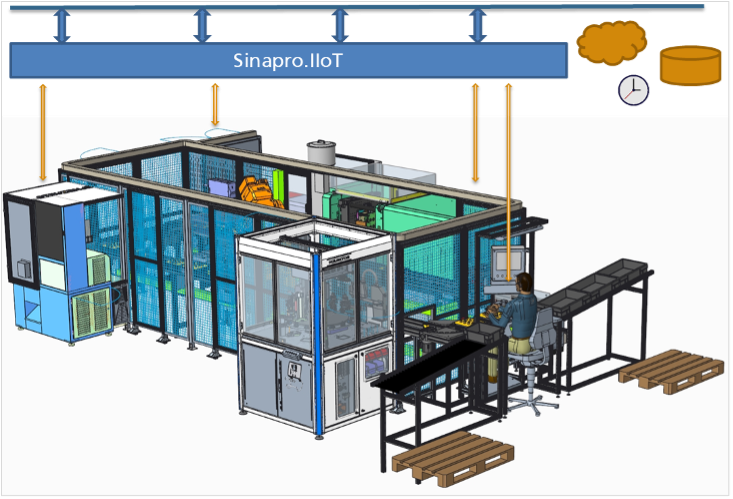
Figure 1: Kolektor's pilot production line. Injection moulding is the key enabling technology for the production of two different products, rotor and stator. The pilot line components communicate with each other via the Sinapro.IIoT MES solution.
Kolektor participates in the most important European project for autonomous quality and zero-defect manufacturing (ZDM) in Industry 4.0 called Qu4lity. Forty-five partners from 13 European countries, including ABB, Siemens, Philips, and Continental, are participating in this project.
Qu4lity will demonstrate how European industry can build unique and highly customized ZDM strategies and competitive advantages through an orchestrated open platform ecosystem; automated ZDM components and digital enablers across all phases of the product and process lifecycle. The main goal of the project is to build an autonomous quality model to meet the ZDM challenges in the era of Industry 4.0.
Kolektor is one of the pilot providers of the project, which focuses on manufacturing and production lines where injection molding is the enabling technology. In general, injection molding is a manufacturing process for various parts, from the smallest components to the entire car body panels. Today, companies strive for operational excellence, and the anomalies that can occur anywhere during the injection molding process can cause lower OEE. Kolektor's machine vision platform KiS 4.0 and Sinapro.IIoT are part of the advanced solutions for the digital transformation of small and medium-sized manufacturing companies into smart factories of the future.
One of the critical aspects of ZDM production is the early detection and elimination of defects. The machine vision platform KiS 4.0 provides advanced capabilities for state-of-the-art quality control based on visual information and artificial intelligence. The IoT camera devices are the data providers on one side and the quality control devices on the other. In one direction, the captured data from the devices flows to the machine learning platform via Sinapro.IIoT, and in the other direction, we apply the learned AI models. The whole platform enables users to constantly monitor and improve the performance of the whole system, contributing to the operational excellence of the company.
Machine vision is the key enabling technology for ZDM. The first piece of the pilot line puzzle is rotor assembly quality control. Artificial intelligence-based machine vision confirms the correct assembly of all components before injection molding. To better understand the relationship between process parameters and the quality of the final product, we will use imaging-based material and injection molding quality parameters. To this end, we are developing intelligent agents and building a ZDM control loop.
Figure 2: Pre-moulding assembly check is performed with the help of the machine vision platform KiS 4.0 and the deployed AI models. Smart camera devices are data producers and, at the same are active devices that perform machine vision quality control. Sinapro.IIoT provides the connectivity layer.
Manufacturing companies are struggling to increase productivity and quality on the one hand and reduce downtime and waste on the other. At the same time, they need to optimize labor, inventory, and material costs. It is quite a challenge to manage all this while being flexible to the ever-changing market demands. With the Qu4lity pilot, we are trying to address key KPIs that impact the business goals of industrial companies through smart digitalization and development of Kolektor Digital Platform. Our goal is to improve the Overall Equipment Effectiveness and reduce the scrap rate in the pilot production line with smart digital solutions.
Back